This system is specifically engineered to process post-consumer PET bottles—whether in compressed bales or loose form. It covers a complete processing line that includes debaling, label removal, intelligent optical sorting, wet granulation, hot washing, dewatering and drying, and final flake color/material sorting.
The entire line is flexibly configurable based on raw material conditions and desired output specifications. It is widely used in PET recycling plants, fiber production facilities, sheet extrusion manufacturers, and bottle-to-bottle recycling projects.
Boxin’s fully automated PET bottle washing line has been trusted by customers in over 50 countries and regions worldwide.
Thanks to its modular, highly adaptable design, it has earned a strong reputation for delivering stable and efficient solutions, regardless of the complexity of the bottle source, production capacity, or target flake grade.
The Advantages of PET Bottle Washing Line
Modular and Flexible Configuration
The system can be tailored to handle various contamination levels of PET bottles—including clean, mixed, or oil-stained bottles—by adjusting the washing intensity and automated sorting stages accordingly.
Three-Stage Deep Cleaning System
Combines cold washing, hot washing, and friction washing to effectively remove grease, glue, and PVC contaminants, ensuring thorough purification throughout the entire process.
Water- and Energy-Efficient Design
Features a closed-loop water filtration system and high-efficiency dewatering units, significantly reducing water and energy consumption per kilogram of PET flakes.
High-Purity Final Flakes
Achieves an exceptionally high cleaning rate with residual impurities controlled to ≤ 100ppm, meeting food-grade and filament-grade recycling standards.
Standard process of PET Bottle Washing Line
From Baled Bottles to Clean PET Flakes
A high-performance PET bottle washing line transforms post-consumer or post-industrial PET bottles into clean, decontaminated flakes ready for reuse.
The entire process consists of a series of mechanical, thermal, and chemical steps, each designed to progressively remove specific types of contaminants. Below is a detailed process flow of Boxin Machinery’s modern washing line, engineered for efficiency, durability, and regulatory compliance.
|
|
|
|
1.Debaling Unit
The debaling system serves as the starting module of the PET bottle washing line. It is responsible for automatically breaking down compressed PET bottle bales and ensuring consistent feeding into downstream equipment. This is a critical unit for operations handling high-density bottle sources, helping maintain smooth and continuous production.
Key Features:
Dual-axis tilt design combined with twin powerful shredding shafts effectively breaks apart even ultra-high-density bottle bales without jamming.
Works in tandem with a chain plate conveyor for stable and regulated material feeding.
Energy-efficient operation, adaptable to varying bale densities across global markets.
Recommended Applications:
Ideal for high-capacity PET recycling lines dealing with tightly compressed bottle bales.
Suitable for facilities that require high production continuity and precise feeding rhythm.
Serves as the core front-end unit in fully automated feeding systems.
|
2.Screening Unit
The trommel screening system acts as the first barrier against contaminants in the PET bottle washing line. It is specifically designed to remove large foreign particles such as sand, stones, glass, and metals that may be mixed into compressed PET bales. By doing so, it helps prevent damage or clogging in downstream crushing and washing machines, serving as a critical "filtration shield" that ensures the smooth operation of the entire production line.
Key Features:
Rotating drum design enables continuous tumbling and screening for high-efficiency contaminant removal.
Equipped with a dual collection system for separate recovery of stones, glass, and metals.
Significantly reduces impact from hard contaminants, extending the lifespan of critical components like crushers and washers.
Anti-blockage design specially reinforced for PET bales imported from regions with high impurity content.
Recommended Applications:
Ideal for processing PET bottles sourced from regions with complex contamination, such as Southeast Asia and South America.
Suitable for factories dealing with bottle bales bound with wire or mixed materials.
Best choice for operations looking to minimize crusher blade maintenance and maximize cleaning system uptime.
|
3.Label Separation Unit
Shrink sleeve labels on PET bottles are one of the most challenging impurities to handle in a PET bottle recycling line. Boxin’s label removal system features a large-diameter cutting rotor with low-speed rotation, enabling high-efficiency label stripping without damaging the bottle body. This greatly enhances both the cleaning performance and purity of the final PET flakes.
Key Features:
Patented Rotor Design:
The large-diameter, low-speed blade rotor precisely cuts and separates shrink labels while avoiding cracks or damage to the bottle structure.
Integrated Label Collection System:
A built-in air-blown conveyor system collects stripped labels efficiently. Collected labels can be resold as a by-product, adding value to the process.
Optional Module:
If your PET feedstock consists of pre-cleaned bottles with no labels, this unit can be skipped as per production needs.
Recommended Applications:
Processing lines with a high ratio of shrink-labeled bottles, especially with PVC content.
Food-grade PET recycling operations where flake cleanliness is a top priority.
Enterprises aiming to improve flake color clarity and reduce impurity levels.
|
4: Manual Sorting Unit
While optical sorting systems offer a high level of automation, manual sorting remains essential for catching what machines might miss. This module serves as a final quality control checkpoint before the crushing process. It works in conjunction with metal detection equipment and manual inspection platforms to remove any remaining off-color bottles, multilayer bottles, or metal contaminants that escape automated sorting.
Key Features:
Fills in Optical Sorting Blind Spots
Manual inspectors can identify subtle color variations, label residues, and foreign bottles that automated systems may overlook.
Integrated Metal Detection System
A fully automated flip-gate metal separator detects and removes bottles containing hidden metals in real time, preventing equipment damage and downstream contamination.
Ergonomic Steel Platform Design
The platform is built with worker safety and comfort in mind, making it easy to operate, clean, and maintain—suitable for high-throughput environments.
High-Capacity Buffer System
Helps stabilize feed flow in large-scale production lines by buffering incoming materials and compensating for supply fluctuations.
Recommended Applications:
Ideal for regions with lower labor costs or facilities that can allocate staff for manual re-sorting.
Used as a final inspection step to complement optical sorting systems.
Strongly recommended for food-grade or filament-grade recycling operations that demand maximum flake purity.
|
|
|
|
|
5: Crushing Unit
The crushing unit is responsible for reducing whole PET bottles into uniform-sized flakes, preparing the material for deep cleaning. Boxin adopts a wet crushing method, where cleaning water is injected during the granulation process. This not only helps remove surface contaminants but also controls temperature and prevents dust and thermal sticking, easing the burden on downstream washing modules.
Key Features:
Wet Crushing with Integrated Cleaning
Water is injected during the crushing process to enable pre-cleaning, dust suppression, and anti-melting—resulting in cleaner, more stable PET flakes.
High Shear Efficiency Design
The cutting chamber uses a scientifically optimized combination of rotating and fixed blades, ensuring smooth, high-throughput cutting with minimal backflow or clogging.
Reinforced Main Shaft
Built with heat-treated alloy steel, the main shaft is engineered to withstand continuous heavy-duty operation without risk of fracture.
Sealed Cutting Chamber
Designed with a tight sealing structure to prevent material leakage and maintain a clean, safe working environment.
Long-Lasting Wear-Resistant Blades
Equipped with cryogenically treated D2 blades, capable of processing over 800 tons of PET material per set with consistent performance.
Noise Reduction by Design
Integrated soundproofing features reduce operational noise for a safer and more comfortable workplace.
Recommended Applications:
Essential unit in all PET washing lines.
Suitable for PET, HDPE, and PP recycling lines requiring flake size reduction.
Ideal for industrial users who prioritize dust control, blade durability, and low maintenance frequency.
Recommended for operations seeking to reduce energy consumption and minimize blade replacement cycles.
|
6: Sink-Float Separation Unit
The sink-float separation unit operates based on the natural density differences among plastics like PET (~1.3g/cm³), PP, and HDPE. In water, PET sinks while PP/HDPE fragments—typically from caps and neck rings—float to the surface. This process enables the efficient physical separation of mixed plastics without the use of chemicals, ensuring an eco-friendly and stable operation.
Key Features:
Accurate Density-Based Separation
Utilizes a fully physical process without chemical additives, delivering environmentally sustainable and highly reliable separation performance.
Modular System Design
Scalable structure allows single-stage or multi-stage configuration based on production capacity, making it easy to adapt to varying processing needs.
Automatic Contaminant Discharge
Floating materials (PP/HDPE) are automatically collected and discharged, enhancing separation efficiency while minimizing manual handling.
By-Product Recovery
Separated PP and HDPE materials can be recycled or sold as secondary raw materials, increasing the marginal economic value of the recycling line.
Corrosion-Resistant Build
Key components are made from stainless steel or coated with anti-rust materials to withstand long-term wet operation conditions.
Recommended Applications:
For PET recycling operations requiring non-chemical separation of bottle fragments and labels.
Ideal for lines that process mixed bottle feedstock and seek to maximize yield and purity.
Suitable for facilities interested in secondary material recovery and value-added by-product management.
|
7: Hot Washing Unit
The hot washing unit is one of the most critical deep-cleaning processes in a PET bottle recycling line. It is designed to remove stubborn contaminants from PET flakes, including grease, adhesives, label residues, and food particles. Boxin’s system utilizes a three-force synergy mechanism—thermal, chemical, and mechanical action—to achieve exceptionally high surface cleanliness standards.
The system supports both two-stage and three-stage tank combinations, with optional timed retention soaking in the second or third stage, ensuring thorough contaminant removal even from heavily soiled PET materials.
Key Features:
Eco-Friendly Alkaline Cleaning Agents
Uses specially formulated, non-toxic alkaline additives to dissolve grease and glue without harming the flakes or the environment.
High-Speed Agitation + Swirl Flow Design
Promotes vigorous flake tumbling and friction, accelerating impurity detachment for more efficient washing.
Flexible “1+2” or “2+1” Tank Configurations
Adaptable to varying contamination levels, with adjustable retention times to optimize cleaning performance.
Closed-Loop Filtration System
Allows filtered cleaning solution to be reused, reducing chemical consumption, water use, and operational costs.
Stable Output Quality
Enhances flake clarity and consistency, minimizing yellowing and surface defects for food-grade or high-end applications.
Optional Temperature Control and Auto-Dosing System
Supports constant temperature maintenance and automated chemical dosing for simplified operation and consistent results.
Recommended Applications:
Essential for bottle-to-bottle, food-grade, and filament-grade PET recycling operations.
Best suited for lines processing heavily contaminated or post-consumer PET feedstock.
Ideal for facilities prioritizing cost control, reliable cleaning results, and environmental sustainability.
|
8: Continuous Rinsing & Friction Washing Unit
After hot washing, PET flakes may still carry alkaline residues and minor impurities. Boxin's three-stage physical purification system—combining friction washing, float rinsing, and 360° spray cleaning—ensures deep, multidimensional cleaning from every angle.
This unit employs multi-stage washing, controlled pH neutralization, and repetitive mechanical agitation to guarantee that no chemical residues remain on the PET flakes. The output meets the high standards required for direct pelletizing, fiber spinning, or bottle-grade applications.
Key Features:
Precise pH Neutralization
Multiple rinsing stages ensure the surface pH of flakes approaches neutral (pH ~7), preventing further oxidation or degradation during downstream processing.
Dual-Speed Friction Washing
Combines high-speed and low-speed friction zones to mechanically remove residual glue, alkali, and embedded dirt particles.
360° Spray Rinse System
Full-coverage spray nozzles deliver dead-zone-free washing, ensuring the highest level of flake surface purity.
Low Water Consumption
Integrated with Boxin’s closed-loop water recycling system, achieving over 50% water reuse rate to reduce operating costs and environmental impact.
Enhanced Clarity & Surface Quality
Efficient removal of visual contaminants significantly improves flake transparency, making the material suitable for clear packaging and premium-grade applications.
Recommended Applications:
Compatible with all PET bottle washing lines, especially those requiring high levels of purification.
Ideal for bottle-to-bottle, pelletizing, and fiber-grade recycling where strict pH control and surface cleanliness are essential.
Recommended for clients targeting high-value transparent applications or direct downstream production.
|
|
|
|
|
9: Dewatering & Drying Unit
After rinsing and friction washing, PET flakes typically retain about 3% surface moisture. The Boxin dewatering & drying unit uses a two-stage process to reduce moisture content to below 1%, meeting the strict requirements of high-grade pelletizing, bottle-to-bottle, and fiber-grade applications.
Key Features:
Two-Stage Drying Process
Centrifugal Dewatering System: High-speed spinning removes most surface moisture, reducing levels to 1.5%–3%.
Hot Air Pipe Drying System: Heated airflow is passed through a pipeline to evaporate residual moisture, achieving final moisture content <1%.
Patented Dewatering Shaft Design
Engineered for stable, clog-free operation, ideal for high-throughput, continuous production environments.
Energy-Efficient Heat Exchange
Optimized hot air circulation minimizes heat loss and lowers energy consumption, contributing to long-term operational savings.
Recommended Applications:
For any PET recycling line targeting pelletizing, sheet extrusion, or food-grade applications requiring strict moisture control.
Ideal for plants with large-scale continuous production, where low maintenance and energy efficiency are priorities.
Essential for meeting export standards and ensuring flake processability in downstream extrusion or injection processes.
|
10: Dust & Light Impurity Removal Unit
After PET flakes have been thoroughly washed and dried, small amounts of label scraps, dust, soft films, and micro-fragments may still remain. Boxin’s dual-stage impurity removal system integrates a Z-type air separation unit and a high-frequency vibratory screen to ensure that PET flakes reach the purity level required for premium applications such as bottle-to-bottle recycling, food-grade pelletizing, and sheet extrusion.
Key Features:
Z-Type Air Separation System
Precisely removes lightweight contaminants such as dust, label flakes, floating films, and ultra-light PP/PE particles by adjusting airflow dynamics and leveraging gravity settling—ensuring high flake purity.
High-Frequency Vibrating Screen
Multi-layer screen decks separate flakes by particle size, efficiently screening out undersized particles, soft materials, and fine contaminants.
→ Improves downstream melt consistency and protects extruders from clogging and screw wear.
Low Energy, High Efficiency
The air separation unit supports variable frequency control, making it adaptable to varying raw material conditions while minimizing energy usage.
The compact, modular structure enables easy integration, cleaning, and maintenance.
Scalable Modular Design
Screen layers and air channels can be expanded according to capacity needs, making the system future-proof and upgrade-ready.
Recommended Applications:
Essential for PET recycling operations targeting food-grade, sheet-grade, or bottle-to-bottle production standards.
Ideal for facilities requiring ultra-clean flakes for downstream extrusion, injection molding, or fiber applications.
Perfect for lines looking to maximize flake quality while minimizing energy use and maintenance downtime.
|
11: Optical Sorting Unit for PET Flakes
After cleaning and drying, PET flakes may still contain trace impurities—including off-color flakes, foreign polymers, aluminum particles, and oxidized/yellowed flakes—that are difficult to detect manually. To meet strict food-grade and high-end recycling standards, Boxin offers an integrated, multi-dimensional optical sorting solution that ensures every flake meets the target quality level.
Key Features:
Triple-Layer Intelligent Detection System
Color Recognition (Color Sorter): Removes off-color flakes to ensure optical consistency.
Material Recognition (NIR Module): Detects and ejects non-PET materials such as PVC, PP, or multilayer fragments.
Eddy Current Separator: Targets aluminum particles and foil contaminants, ensuring full metal decontamination.
→ These modules can be custom-configured to meet different purity thresholds and product specifications.
Aging Flake Detection Algorithm
Advanced recognition of yellowed, oxidized, or high-melting-point flakes, improving melt consistency and quality stability in downstream pelletizing or extrusion.
Recommended Applications:
Bottle-to-bottle, food-grade, and high-clarity film/sheet production requiring ultra-high purity.
Ideal for operations aiming to maximize final product value by eliminating visual and chemical contaminants.
Suitable for automated recycling lines where manual sorting is insufficient to meet export or FDA-level standards.
|
12: Bagging & Packaging Unit
At the final stage of the PET washing process, high-purity PET flakes are automatically conveyed via air transfer systems into the bagging unit. This module allows for automated metering, controlled discharge, and precision packaging, ensuring efficient product handling and stable output quality.
Key Features:
High-Speed Automated Bagging
Significantly reduces manual intervention while improving efficiency in final product handling and shipping.
Smart Weighing & Bagging System (optional)
Optional integration of intelligent weighing units enables precise per-bag dosing, supporting consistent batch tracking and quality assurance.
Recommended Applications:
Essential for PET recycling facilities requiring automated discharge, packing precision, and production monitoring.
Suitable for high-throughput operations seeking to reduce labor input and enhance packaging consistency.
|
13:Finished product display
|
|
|
|
Types & Applications of PET Bottle Washing Lines
PET bottle washing lines are not one-size-fits-all—they are engineered in modular or integrated designs based on raw material conditions, capacity goals, and final product applications. Understanding these differences is critical for global buyers to select systems tailored to their needs.
Cold Wash vs. Hot Wash Lines
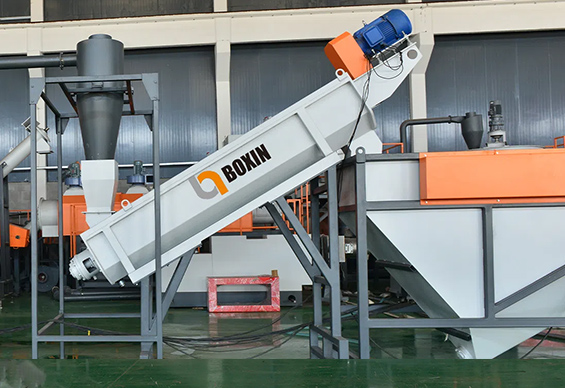
Cold wash lines are mainly used to produce lower-end downstream products such as PET strapping. The system primarily relies on friction and float-sink separation to remove contaminants. While these lines are cost-effective and energy-efficient, the resulting rPET typically has lower market competitiveness.
|

Hot wash lines are designed for post-consumer PET bottles contaminated with grease, organic residues, or adhesives. The process includes a hot caustic wash (commonly using NaOH), which effectively removes organic pollutants. Hot wash units are recommended for all applications beyond basic strapping production.
|
Standard vs. Food-Grade Lines
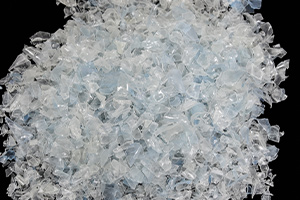 |
Standard PET washing lines generally include hot washing, multi-stage cleaning, centrifugal drying, and optional advanced sorting modules. These are suited for non-food applications such as fiber, injection-molded parts, or sheet extrusion. (See: Fiber Grade PET Bottle Washing Line)
|
Modular And Turnkey Configurations
Modular washing lines offer layout flexibility and staged expansion, ideal for recyclers in developing regions or those anticipating future growth.
Turnkey washing lines are fully integrated, pre-tested systems designed for rapid setup, guaranteed performance, and reduced engineering complexity.
Capacity Range & Scale
PET washing lines vary from 500 kg/h pilot-scale systems to 6,000 kg/h industrial lines. Capacity selection affects:
- Total system cost and cost per ton
|
2. Utility consumption (kWh/ton, m³/ton)
|
3. Labor per unit of output
|
4. Flake consistency and quality
|
Boxin Machinery custom-builds lines across all capacity levels and provides pre-sales engineering support to match buyer-specific input material and output requirements.
Pricing and Cost Considerations in PET Recycling Lines
Pricing for PET bottle washing lines varies significantly depending on several factors:
-
Capacity (e.g., 500 kg/h vs. 5,000 kg/h)
-
Hot washing inclusion (standard vs. food-grade output)
-
Level of automation
-
Optional modules (e.g., optical sorters, aging flake removers)
-
Final flake purity targets (e.g., <300 ppm, <200 ppm, <100 ppm)
|
Additional Cost Considerations:
-
Freight cost (FCL shipping)
-
Installation costs (typically 1%–3% of total project value)
-
Water and electricity availability and usage costs
-
Chemical inputs (e.g., caustic soda, antifoam agents)
|
Buyers should calculate key financial indicators including:
-
ROI period based on current rPET market prices
-
Indirect benefits from local environmental tax incentives
-
Labor vs. automation trade-offs
Careful assessment of both capital expenditure and long-term operating costs is essential for ensuring commercial sustainability of the PET recycling investment.
|
Reference FOB Price Range from China:
-
500 kg/h cold wash line: $60,000 – $80,000
-
1,000 kg/h hot wash line: $120,000 – $160,000
-
3,000 kg/h turnkey system: $300,000 – $450,000
|
Project Case Study
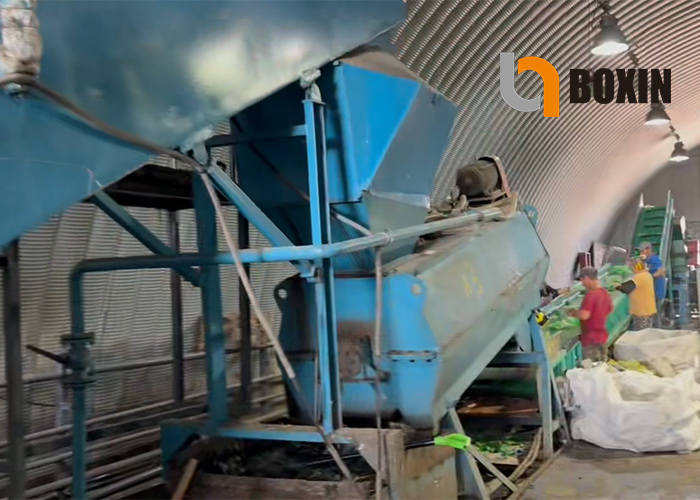
Kazakhstan— 15 Years of Continuous Operation
The client is based in Kazakhstan and is one of the earliest companies to enter the PET bottle recycling industry in the country. As early as 2009, the client purchased a complete PET bottle washing line from our company, Boxin Machinery.
To this day, the production line delivered 15 years ago continues to operate under high load, consistently producing RPET flakes that meet downstream requirements.
|
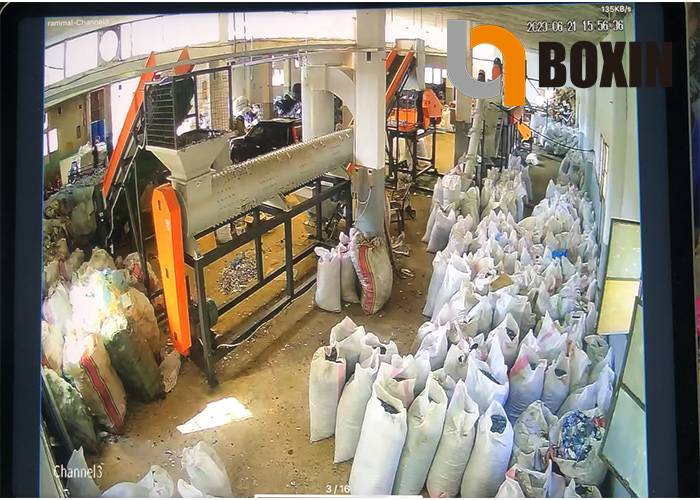
Lebanon
This client is based in Lebanon and has been engaged in plastic recycling trade and processing for a long time, primarily selling baled PET bottles. With the local shift in recycled materials policy, the client decided to invest in building their own PET bottle washing line to increase raw material value and supply local plastic product manufacturers.
|
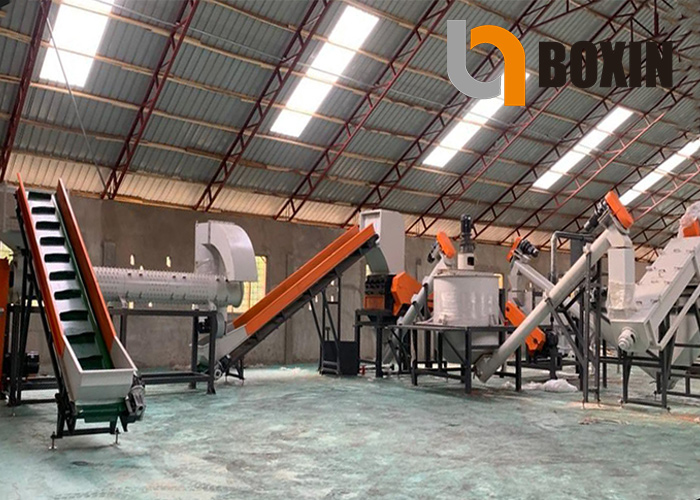
Ghana
This client is based in Ghana and is a local startup engaged in plastic recycling and the sale of recycled materials. With the Ghanaian government promoting the development of domestic recycling industries, the client plans to invest in a complete integrated production line—from PET bottles to recycled pellets.
|
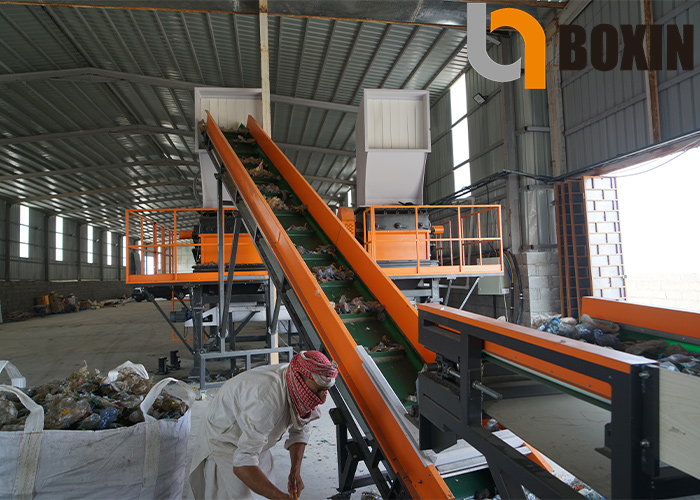
Saudi Arabia
This customer is located in Saudi Arabia and plans to process locally collected waste PET bottles into fiber-grade PET flakes to supply local spinning enterprises.
Customer Type: Plastic recycling factory
|
Custom OEM Services & Solutions
As a professional PET bottle washing line manufacturer in China, Boxin Machinery stands out in the industry with its OEM and custom engineering capabilities. For global B2B buyers, the ability of the system to adapt to local raw material conditions, regulatory requirements, and factory layout is a key factor in procurement decisions.
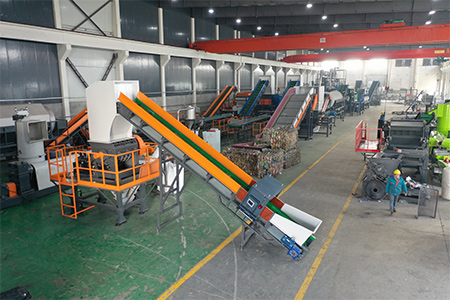
Tailored Engineering
|
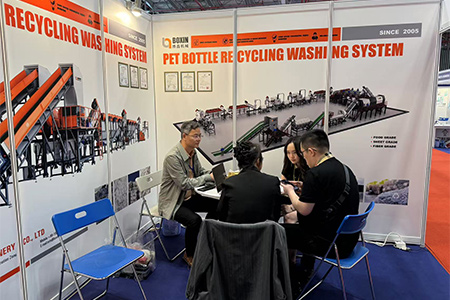
Pre-Sales Testing & Consultation
|
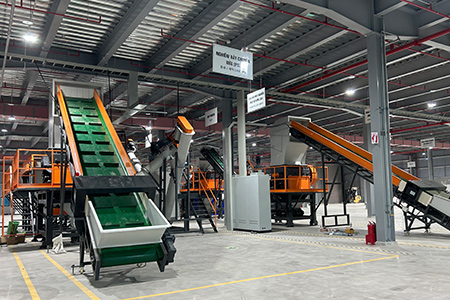
Global Installation & Training Services
|
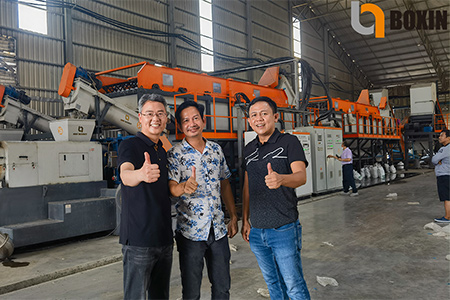
After-Sales Technical Support
|
-
Raw material assessment (via sample analysis)
-
Customized process flowchart and plant layout (CAD drawings)
-
Modular equipment selection based on buyer priorities (cost, output, water resource constraints, etc.)
-
Turnkey delivery including steel platforms, electrical wiring, piping, and control cabinet configuration
|
Clients can send PET bottle samples to Boxin’s R&D center for small-scale washing and contamination analysis. Based on the results, Boxin recommends a suitable system configuration considering:
Contamination type (glue, oil, label type)
Color ratios (clear, blue, green, or mixed)
Moisture levels and target IV retention of flakes
|
Boxin offers on-site installation, commissioning, and operator training, as well as remote installation support via video calls. Buyers will receive:
|
Boxin guarantees:
-
One-year full machine warranty
-
24-hour technical response
-
48-hour dispatch for critical spare parts
-
Lifetime maintenance guidance
|
Industry Knowledge Extension :::
More information about PET bottle recycling Production Line
|
|
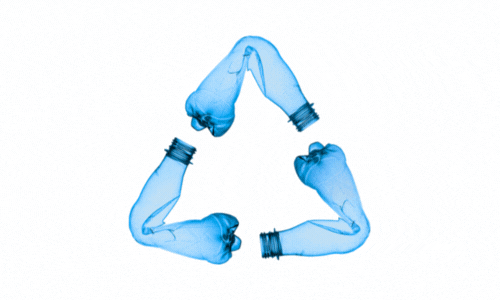 |
Why a PET Bottle Washing Line Is Critical for Modern Recycling Operations
1. Global PET Consumption & Waste Challenges
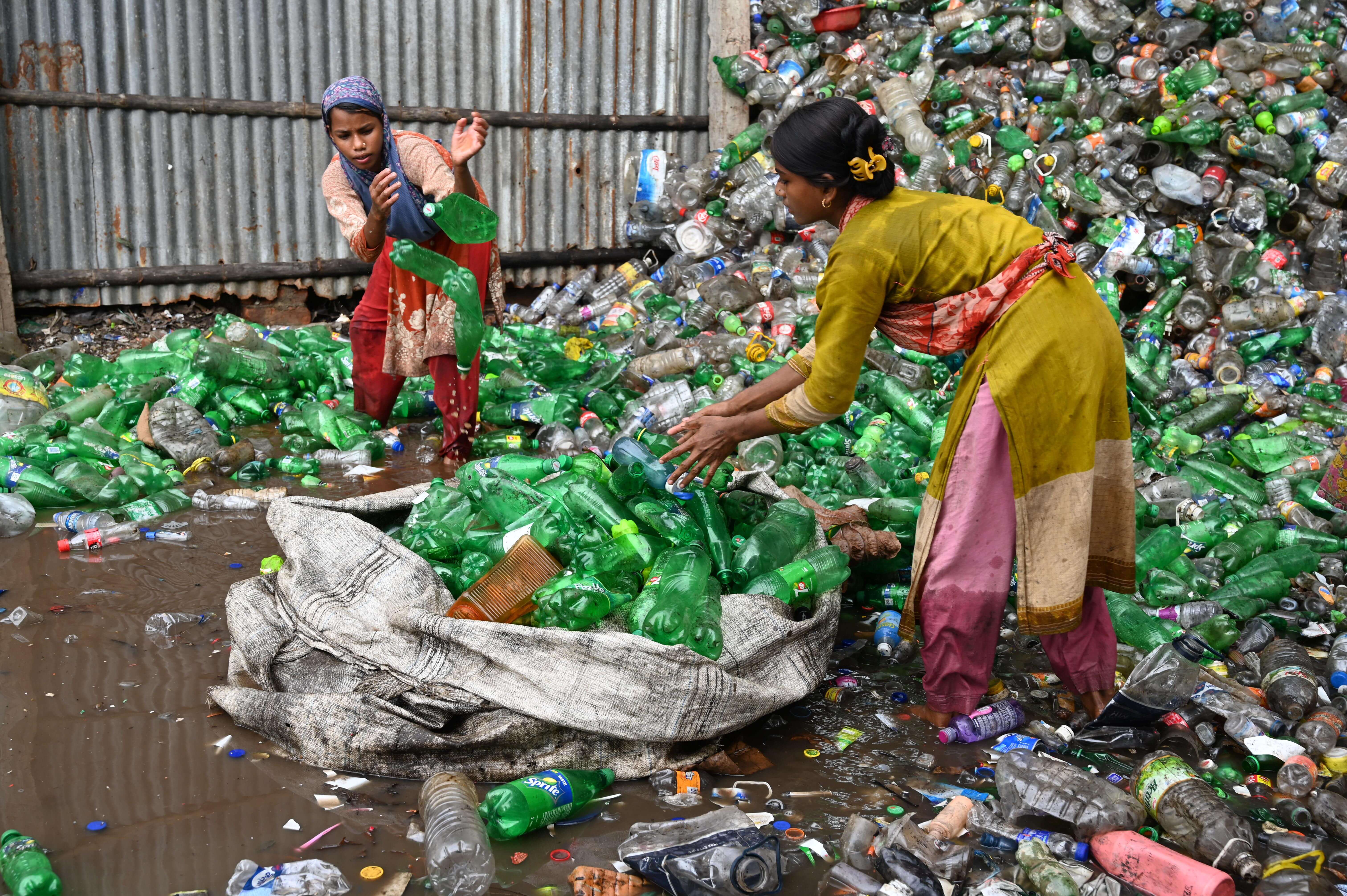 |
Polyethylene terephthalate (PET) remains the fastest-growing packaging polymer, with global demand exceeding 43 million tonnes in 2024—roughly double the volume from a decade ago.
However, according to the World Bank’s What a Waste 2.0 database, less than one-third of post-consumer PET bottles are collected for recycling on average, and only a small portion reaches food- or fiber-grade quality. This widening gap between consumption and closed-loop recycling capacity is placing mounting pressure on brands, regulators, and recyclers to adopt more efficient and scalable washing technologies. |
2. How PET Bottle Washing Lines Drive the Circular Economy
A PET bottle washing line is a fully integrated system that converts baled or loose PET waste into contaminant-free, high-purity flakes while preserving intrinsic viscosity (IV). These flakes are ready for direct extrusion, pelletizing, or bottle-to-bottle solid-state polycondensation (SSP).
Properly configured washing lines can reduce glue, PVC, and aluminum content to below 100 ppm—meeting FDA and EFSA food-contact standards. By producing high-purity flakes locally, converters can reduce reliance on virgin resin, cut greenhouse gas emissions by up to 70%, and comply with increasingly strict recycled-content mandates in the EU, USA, and ASEAN.
3. Key Drivers for Investing in Advanced Washing Systems
-
Regulatory Pressure: From the EU Single-Use Plastics Directive to California’s SB 1013, legislation is increasingly linking market access for beverage bottles to minimum rPET content (EU target: 25% by 2025). Plants without food-grade washing capabilities risk being phased out.
-
Market Incentives: Over the past 18 months, rPET pellet prices have averaged 14–22% higher than virgin PET, rewarding recyclers who can deliver consistent quality and IV retention.
-
Operational Efficiency: Next-generation friction washers and closed-loop filtration systems reduce water usage to under 2 L/kg. Energy-efficient high-speed dryers cut power consumption to as low as 0.28 kWh/kg.
4. Why Choose Boxin Machinery as Your China-Based Custom Supplier
Founded in 2005 and headquartered in Zhangjiagang, Boxin Machinery operates a 12,000 m² advanced factory and has delivered over 80 turnkey PET bottle washing lines worldwide, including FDA-compliant rPET projects in the USA, Chile, Saudi Arabia, and Vietnam.
Its modular design philosophy allows buyers to customize debaling, hot wash, and optical sorting stages based on input bottle characteristics and product targets—ensuring optimal price-performance ratio and long-term cost control (with equipment lifespans of up to 15 years).
FAQ & Expert Tips: Most Common Buyer Questions
Straight Answers to the Questions You Might Be Hesitant to Ask
What is the minimum order quantity (MOQ) for a PET washing line?
A complete system starting from 500 kg/h. However, if the budget allows, a 2,000–3,000 kg/h system is recommended for better ROI.
What is the standard lead time?
40–60 days depending on customization level.
Can both clear and colored bottles be processed together?
Yes, but since downstream uses differ, an optical sorter is recommended for color separation.
Is hot washing necessary?
It is strongly recommended for all applications except PET strapping production.
How much water is consumed by the system?
With a closed-loop water recycling system, consumption is 1.5–2.5 m³ per ton of PET.
What chemicals are used in the washing process?
Mainly caustic soda and antifoaming agents; surfactants are used in some cases.
Does Boxin provide training?
Yes, both on-site and remote training are included in the turnkey service.
Can the system handle oily or contaminated bottles?
Yes, as long as it includes hot washing and high-speed friction modules.
What is the power consumption of the system?
Depending on the setup, energy use ranges from 0.28 to 0.45 kWh per kg of PET.
What after-sales support is offered?
One-year full machine warranty, 24/7 technical response, 48-hour dispatch of critical parts (excluding custom items), and lifetime maintenance guidance.