Before recycling, these films typically need to be sun-dried and repeatedly turned over to remove soil, yet they often still retain more than 30% of wet mud and impurities. This is especially true after the planting season, when black mulch films are tightly bonded with the soil—one side coated with wet earth, while the other may carry residual fertilizer granules and pesticides. Greenhouse films, though thicker, are prone to surface contamination such as accumulated dust, condensed water droplets, bacterial mucus, and pesticide residues from spraying.
The variety and nature of these contaminants are highly complex. Large sand and soil particles require mechanical shaking; highly adhesive residues and oily mud need intensive friction or high-temperature dissolution; water-soluble fertilizers and polar pesticides may require chemical neutralization or multiple rinsing stages to be effectively removed.
These contamination characteristics determine the complexity of the washing process: it must involve stepwise pre-washing, friction scrubbing, thorough float-sink separation, and chemical treatments to ensure the removal of most impurities. Otherwise, wastewater containing sand and contaminants cannot be properly discharged, and the quality of subsequent pelletizing will be difficult to guarantee.
Key Equipment and Functions of Agricultural Film Washing Line
|
|
|
|
1.Feeding & Crushing System
Transports raw film material steadily to the crusher and pre-shreds it into 50–60 mm flakes, making it suitable for downstream washing processes.
Key Features:
Compact structure with small footprintEnsures continuous and stable feedingFitted with D2 wear-resistant alloy blades for extended lifespanSpecially adapted for highly contaminated flexible film materials
|
2. Friction Washing Unit
Removes stubborn contaminants through multi-stage high- and low-speed friction cleaning.
Key Features:
Multi-zone friction cleaning design
Anti-wrapping mechanism protects machine and materials
Ensures strong cleaning power while maintaining film integrity
|
3: Sink-Float Separation Tank
Separates out heavy contaminants such as metals, sand, and other dense residues using water-based density separation.
Key Features:
Equipped with multiple rotating rollers for continuous impurity discharge
Efficient sludge removal system to prevent blockages
Stable, high-efficiency operation with enhanced decontamination results
|
4: Film Dewatering & Drying Machine
Combines mechanical squeezing and thermal drying to produce semi-molten flakes with moisture content <5%, ready for pelletizing.
Key Features:
Centrifugal dewatering + screw squeezing + hot air drying
Ensures stable semi-plasticized output quality
Optimized for direct pelletizing applications
|
|
|
|
|
5:Finished product display
|
|
|
|
Differences in Characteristics of Various Agricultural Films and Recommended Washing Configurations
Agricultural films are generally categorized by their source into mulch films (black films covering the ground) and greenhouse films.
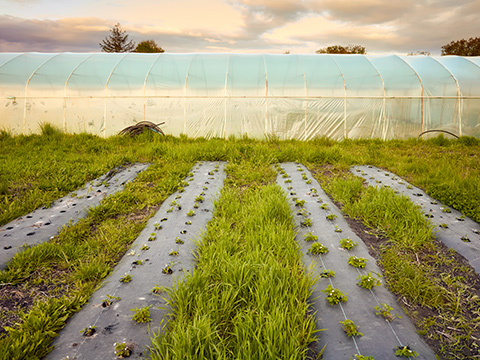 |
Mulch Films
Mulch films are typically thinner, with a thickness ranging from 0.008 to 0.02 mm, and have large contact areas with soil. The main contaminants are adhered fine sand and soil, along with small amounts of fertilizer and pesticide residues.
Recommended washing configuration:
Multi-stage friction washing and sedimentation separation systems.
For mulch films with high mud and sand content, it is advisable to add bottom screw discharge systems for better sediment removal.
Additional sun-drying and soil-shaking steps are recommended to remove large soil clumps before entering the recycling line.
|
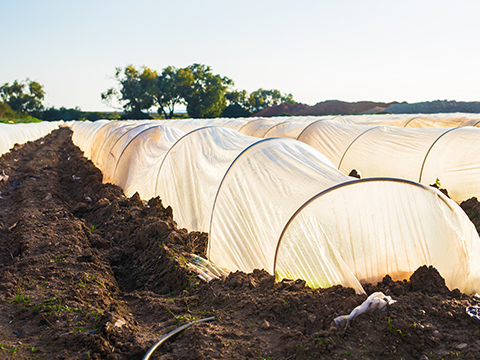 |
Greenhouse Films
Greenhouse films are usually thicker and more durable (typically 0.08 to 0.12 mm or even thicker), with a service life of 1 to 3 years. The surface is often covered with dust and condensation stains, and films near the greenhouse structure may also be contaminated by spider webs, biofilms, and algae.
Recommended washing configuration:
Less reliance on sedimentation (since soil contamination is minor).
Greater emphasis on chemical additives and temperature control.
It is recommended to add alkaline or oxidizing agent treatment tanks during the rinsing stage to help break down pesticides and organic stains.
|
Common Bottlenecks and Optimization Recommendations
During actual operation, agricultural film washing lines often face the following common issues:
1. Sand clogging: pipelines, screens, and nozzles are frequently blocked by sand particles. 2. Blade wear: crusher and shredder blades quickly become dull in sand-rich environments. 3. Turbid rinse water: rinse water remains cloudy with fine mud particles. 4. Capacity reduction: equipment blockages or insufficient pre-treatment lead to decreased processing efficiency.
Technical Optimization Recommendations:
1. Automated Sludge Discharge: Install spiral discharge systems at the bottom of sedimentation tanks to enable continuous sludge removal and online cleaning.
2. Blade Material and Coating Upgrades: Use high-hardness alloy steel blades (D2) with surface strengthening treatments (cryogenic treatment) to significantly improve wear resistance and impact durability, thereby extending blade life. Adopt double-edged reversible fixed blades in design to reduce downtime and maintenance costs.
3. Wastewater Treatment Optimization: Rinse water often contains suspended solids and colloids. Without proper treatment, directly recycling the wastewater will negatively affect subsequent cleaning stages. It is recommended to add filtration and clarification systems to ensure water quality.
Customized Service
At Boxin, we understand that every client’s raw material conditions and production goals are unique. There’s no need to worry if the above process modules seem complex or not entirely applicable to your situation.
we specialize in customizing process flows and equipment combinations based on your specific input material—whether your Recycled raw materials vary by origin, contamination level.Simply provide us with a sample of your raw material or the basic technical parameters, and our engineering team will design the most suitable Platic recycling solution for your needs.