The machine is capable of processing a variety of plastic raw materials and forms. It supports common thermoplastics such as PE、PP、PVC、ABS、PS and more, including both post-industrial scraps and post-consumer plastics.
Typical feed materials include plastic bottles (PET drink bottles, HDPE containers), plastic pipes and profiles, plastic drums or buckets, films and sheets, and even thick lumps or purgings from extrusion or molding processes. Thanks to its robust cutting system, the grinder can handle different sizes and shapes of plastic waste with high efficiency.
Working Principle & Structure
Plastic waste is fed into the grinder’s cutting chamber, where rotating knives on a rotor shred the material against stationary knives mounted on the chamber wall. The process involves cutting, tearing, and shearing actions that gradually reduce the plastic pieces to the desired size. A screen beneath the rotor ensures only particles small enough (per the chosen mesh size) pass through, yielding uniform regrind. Oversized pieces remain inside until further cutting occurs. Once shredded to the proper size, the granulated plastic is discharged, often by an integrated conveyor or blower, for collection or downstream processing.
Structure: A complete plastic grinding machine system typically includes several modules:
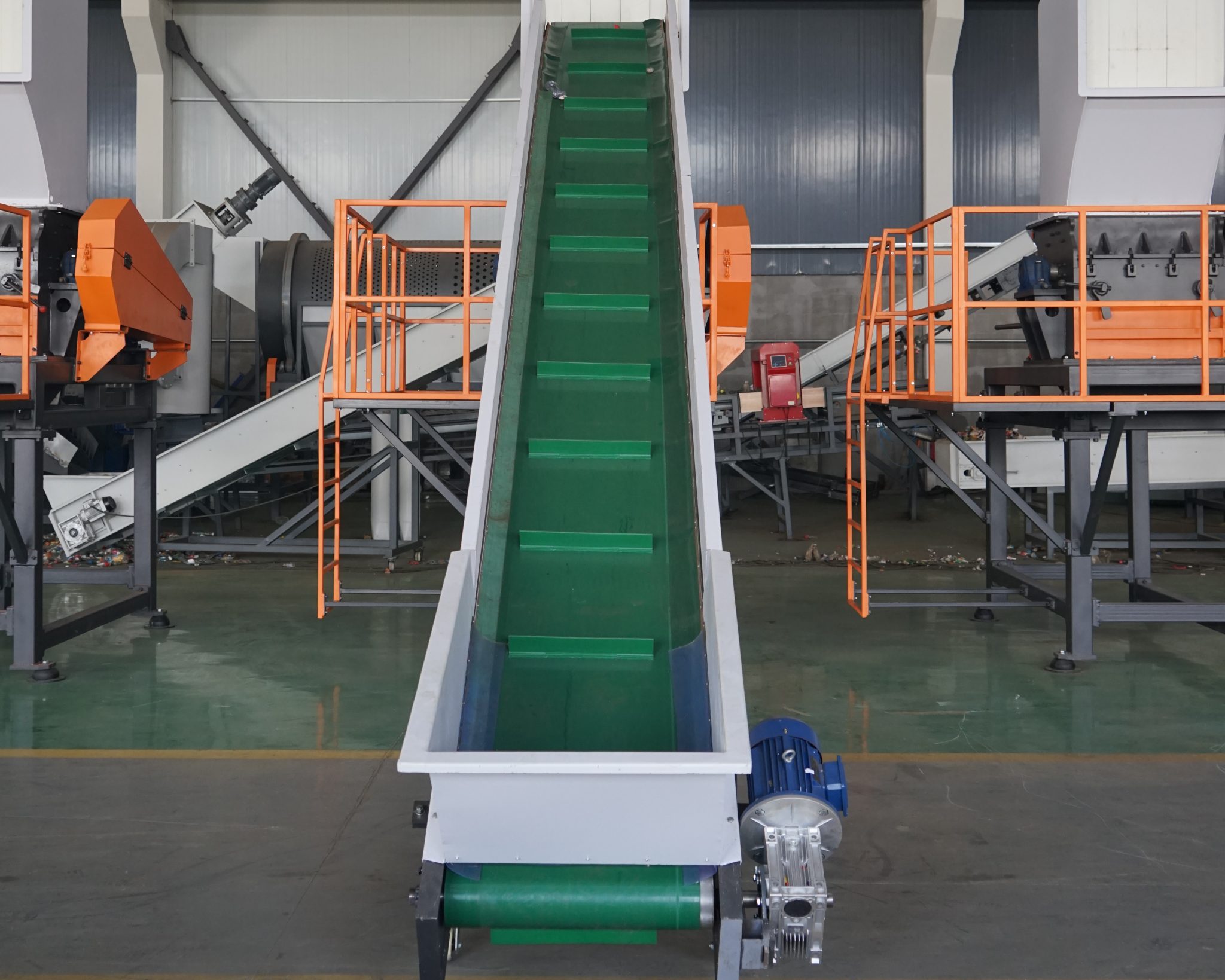 |
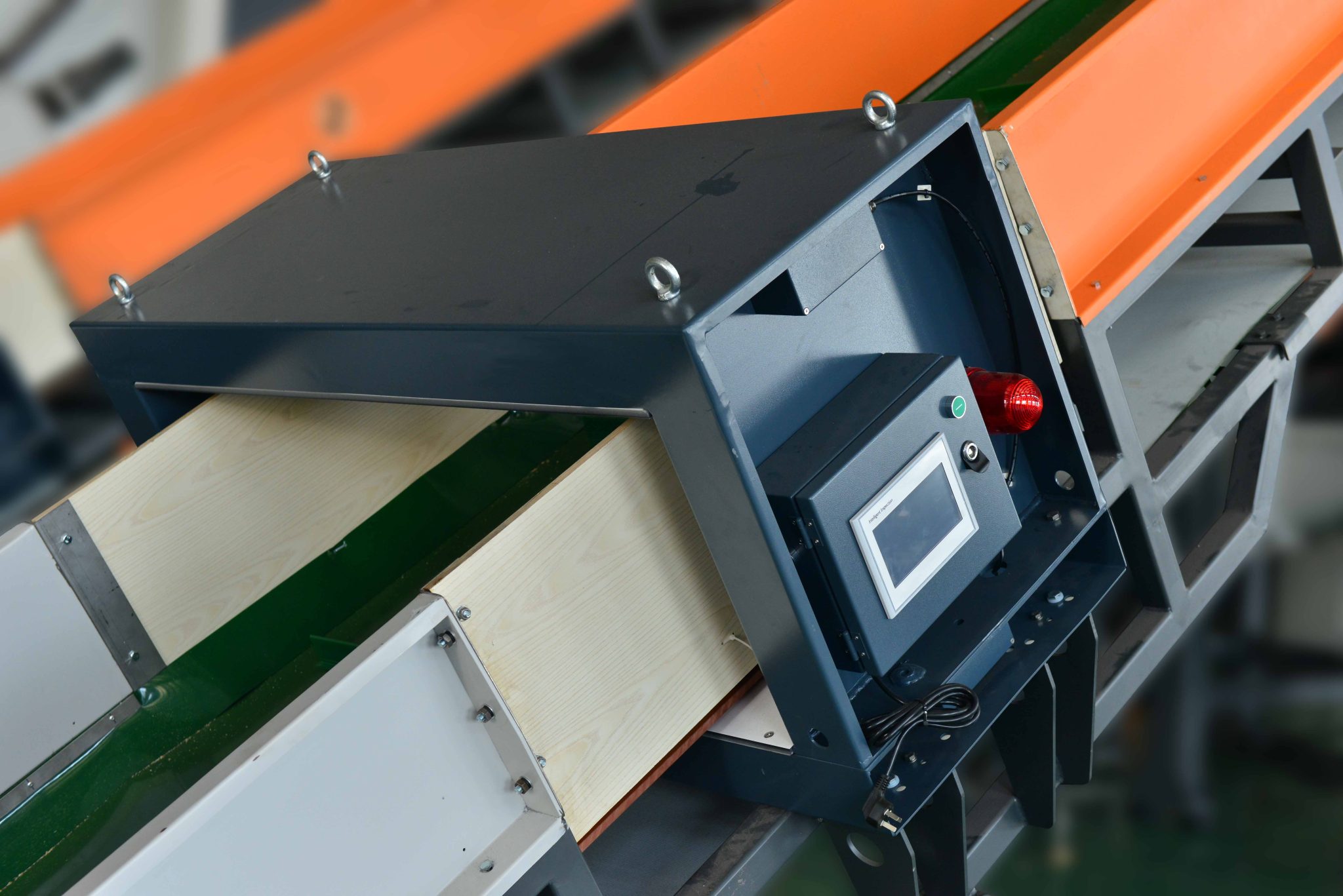 |
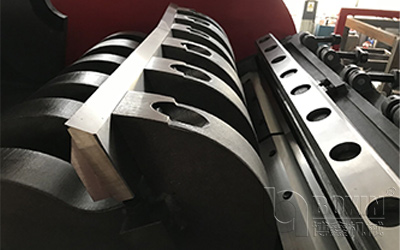 |
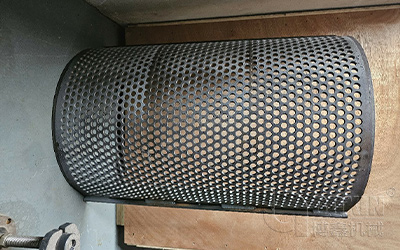 |
A belt conveyor can continuously deliver scrap into the crusher. Advanced systems use an automatic feed control – for example, adjusting belt speed based on crusher load – to ensure continuous, efficient feeding without overloading
|
Metal Detector :
An optional metal detector or magnetic separator is installed on the inlet conveyor to detect and remove any metal contaminants before they enter the cutting chamber This protects the blades from damage if nails, bolts, or other metals are mixed in the scrap.
|
Cutter Chamber & Rotor :
The core of the machine is the cutting chamber housing a heavy-duty rotor (knife holder) with multiple rotary blades and fixed counter-blades. The rotor is engineered with a V-shaped knife arrangement for slicing efficiency and a scissor-like cutting action. As the rotor spins at high speed (driven by an electric motor and belt drive), the knives continuously chop the incoming plastic against the fixed knives, rapidly reducing its size.
|
Screen Sieve:
A replaceable screen with specified hole diameter sits below the knives. It ensures consistent output granule size – common mesh sizes range from a few millimeters up to ~50mm, depending on the desired flake size. The screen frame can often be opened or removed easily (sometimes via hydraulic mechanisms in larger models) for cleaning and maintenance.
|
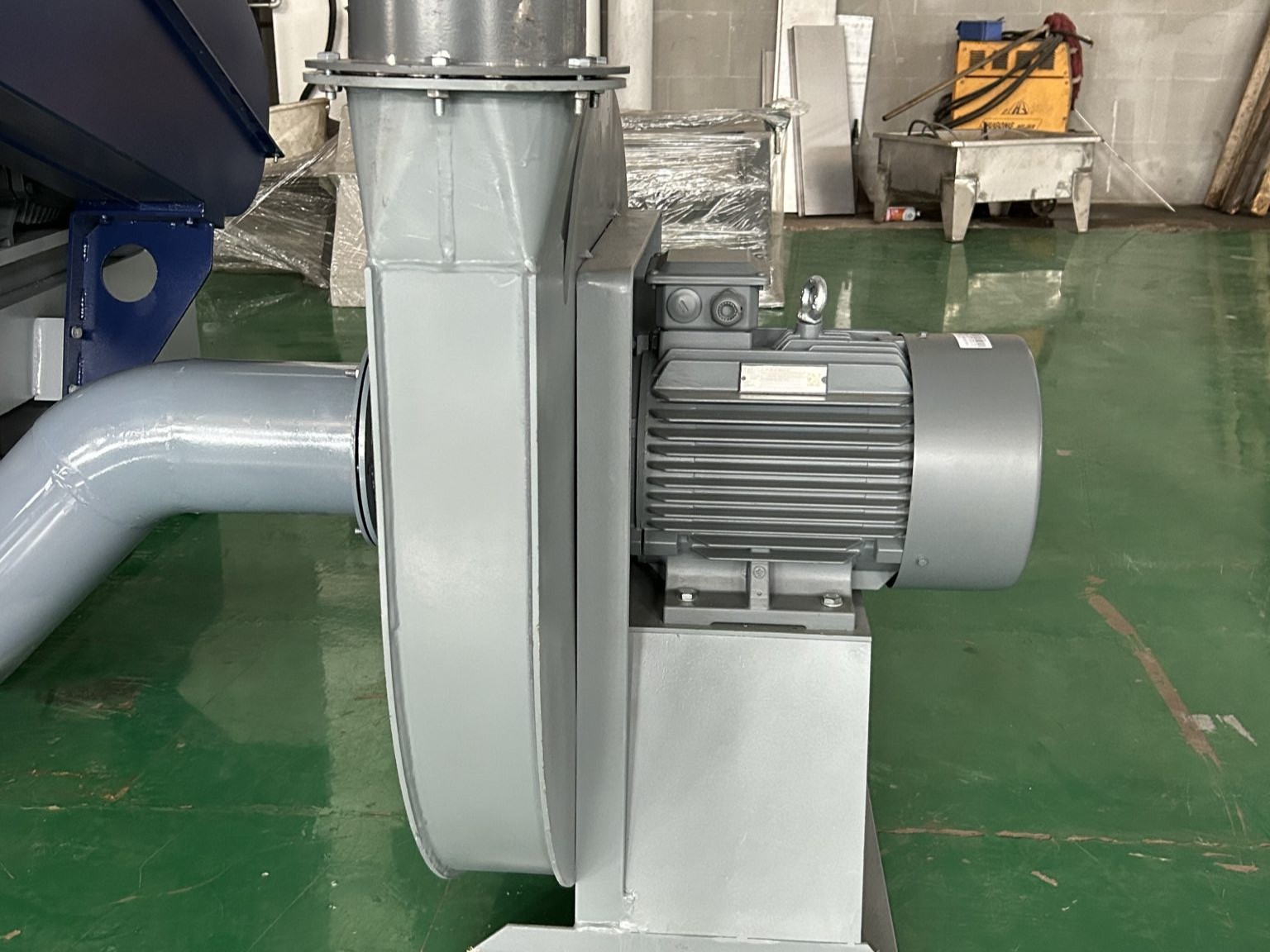 |
|
|
|
Discharge System :
After crushing, the output plastic flakes are expelled from the chamber. Depending on configuration, this may be a gravity outlet (dropping into collection bins or bags) or an air conveyor system that pneumatically transports the regrind to a storage silo or next processing step. Many systems include a blower and cyclone separator to convey and simultaneously cool the material, as well as to remove dust for a cleaner output.
|
|
|
|
Technical Features
 |
The blades are made from cryogenically treated D2 steel, giving them outstanding wear resistance and durability. This keeps the knives sharp even when processing highly abrasive materials, reducing the need for frequent blade changes. |
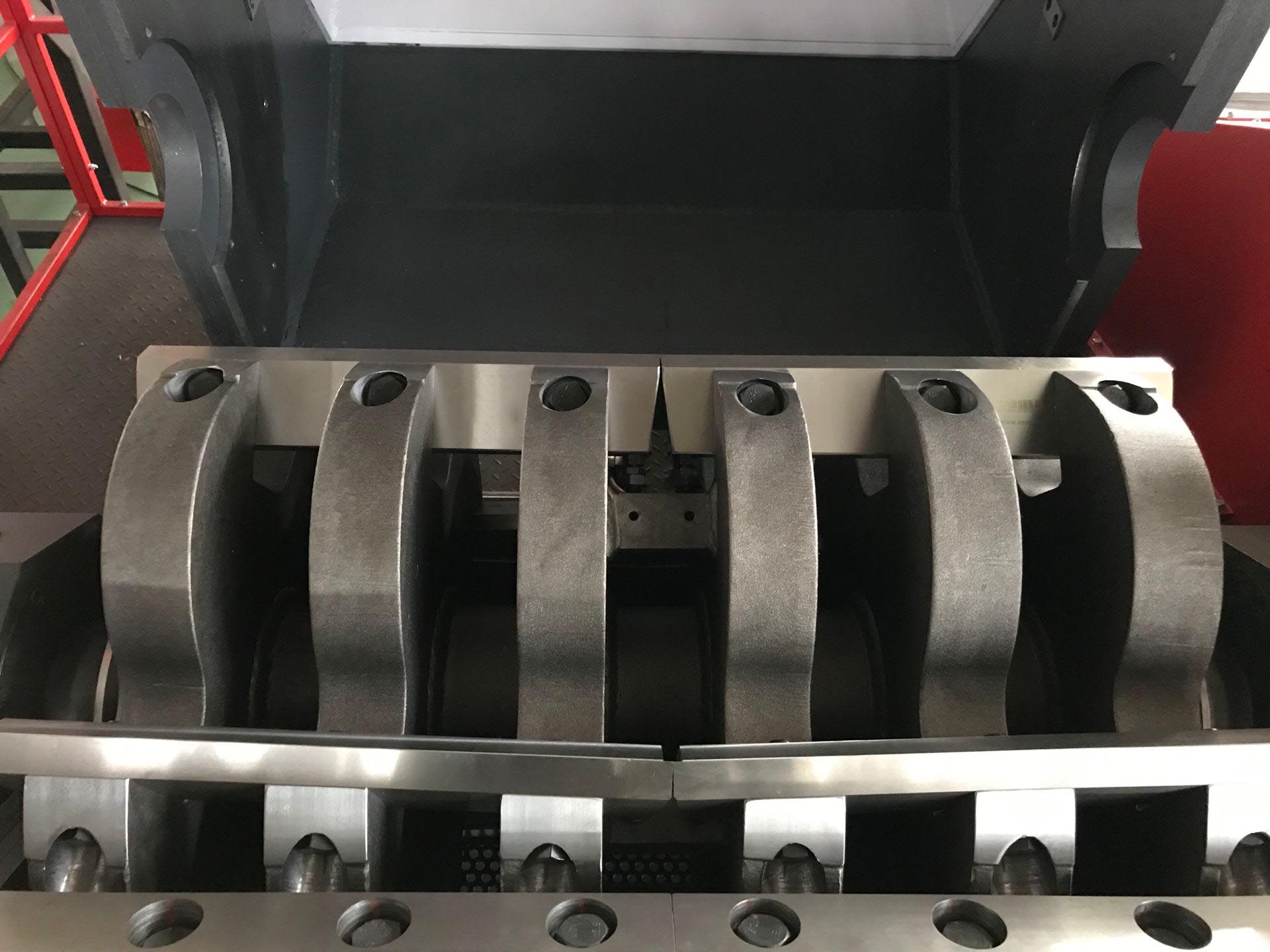 |
V-Shaped Cutter Assembly: The rotor knives are arranged in a “V” formation (or staggered scissor arrangement), which improves the cutting efficiency and produces uniform granules while reducing impact and noise. This design draws the material toward the center and distributes the cutting action, leading to smoother operation. |
High Throughput & Efficiency: Engineered with powerful motors and optimized cutting geometry, the machine achieves high output rates to meet industrial scale recycling. Depending on model and material, capacity can reach hundreds of kilograms per hour – for instance, heavy-duty crushers can process up to 1000 kg/h of plastic waste. The efficient cutting action and continuous feeding system ensure maximum throughput with minimal energy waste.
Low Noise Operation: The grinder is designed with noise reduction in mind – features like a double-layer soundproof hopper, shock-absorbing mounts for the motor and frame, and a precision-balanced rotor all help to minimize vibration and noise. Typical operating noise levels can be as low as 85 dB or below under full load, meeting environmental and workplace safety requirements. This quieter operation creates a better working environment for operators.
Modular & Robust Structure: The machine features a modular design where components like the rotor, blades, screen, and motor are designed for easy disassembly and replacement. The housing and cutting chamber are made of thick, reinforced steel (often with replaceable wear liners) to ensure stability and long service life. This modular build not only makes maintenance easier but also allows customization or upgrades (for example, adding a conveyor, blower, or updated control system as needed).
The machine’s maintenance-friendly design features a dual-hydraulic system: Hydraulic top cover – lets operators safely and quickly change blades and set knife clearance from outside the chamber. Hydraulic pull-out screen drawer – allows a single person to slide the screen out, clear residual granulate, and inspect the interior with ease. These service-oriented details keep downtime to a minimum and maintain continuous, stable production.
Advantages of Clean vs Contaminated Materials
In-House Factory Scrap: Clean plastic scrap generated within a factory – such as sprues, runners, trims, or defective products from injection or extrusion processes – is typically dry, uncontaminated, and uniform in composition.
For these materials, the machine emphasizes high throughput, efficiency, and stable continuous operation. It can be run at higher speeds to maximize output and is built for reliable 24/7 performance with consistent particle size, so that recycled granules can be directly fed back into production. Recycling in-house scrap not only reduces waste but also saves raw material costs – many manufacturers reuse 100% of their recovered plastic in new production. Accordingly, the crusher’s design focuses on productivity and consistency for factory scrap: high-speed cutting for increased capacity, optimized rotor and screen for uniform regrind, and robust motors/gearboxes to handle long hours of operation without overheating.
Post-Consumer & Contaminated Waste : Recycled plastics from post-consumer sources – like packaging waste, used bottles, agricultural film with dirt, or mixed plastic from municipal collections – often come with contaminants (labels, paper, organics), abrasives (sand, glass), and even metallic debris.
To tackle these, the machine is built with extra durability and protective features. Cutting components and the chamber are equipped with wear-resistant materials (e.g. optional hardened steel or ceramic liners that extend the chamber life by 3× when processing sand- or glass-filled plastics) to withstand abrasive impurities.
The rotor operates at a suitable speed and torque to handle tough, impact-prone chunks without damage. Crucially, a metal detection or separation system is integrated to automatically stop or divert metal pieces, effectively preventing metal from entering and damaging the blades. The machine’s structure also includes shock absorbers and overload protection; if an un-shreddable object or excessive load is detected, the system can auto-reverse and stop to avoid failure. In summary, for contaminated “social” waste, the design prioritizes blade and machine protection, wear resistance, and high impact tolerance over pure speed. This ensures safe and continuous processing of dirty plastics that would rapidly wear out ordinary crushers.
Customization & Support
Blade Configurations: The number, shape, and material of blades can be adjusted for the material type. For example, customers can choose knife styles (claw blades, flat blades, V-shape cutters, etc.) and quantity of rotary knives to optimize cutting performance for their particular waste stream.
Screen Mesh Size: We offer screens with various hole diameters to control output size, and these can be easily swapped. Whether you need coarse flakes or fine granulate, the screen size (e.g. 8 mm, 20 mm, 50 mm, etc.) is configurable.
Motor Power and Drive: The machine’s motor size and drivetrain can be selected to match the required throughput and material hardness. Higher horsepower motors or multiple motors can be provided for tough, high-volume jobs, whereas energy-efficient smaller drives can be used for light-duty operations. We ensure that even customized setups use quality motors and gearboxes for longevity.
Additional Features: We support a range of non-standard customizations. Examples include: adding soundproof enclosures for extra noise reduction, water spraying systems for wet crushing if needed, special infeed hoppers or feeding devices (e.g. screw feed for films), and custom paint or stainless-steel construction for food-grade or corrosive environments. Non-standard voltages or motors to suit different countries’ power supply are also available.
Turnkey System Design: Beyond the crusher unit itself, Boxin can design entire recycling systems around it. This might involve pre-shredders, conveyors, washing equipment, silos, etc., configured in a modular way. Our engineering team works with clients to ensure the crusher seamlessly integrates into their production line or plant layout.
Technical Support and Service: Along with customization, we provide full after-sales support. This includes installation and commissioning assistance, training for your operators, and documentation. Spare parts (blades, screens, etc.) are readily available, and our support team is on standby to help with maintenance or troubleshooting. We pride ourselves on responsive service to keep your machine running with minimal downtime.